行业百科
打破壁垒,构建整车研发CAE数据协同平台
一、企业简介
奇瑞汽车股份有限公司(以下简称“奇瑞”)成立于1997年1月8日。公司成立21年来,始终坚持自主创新,逐步建立起完整的技术和产品研发体系,产品出口海外80余个国家和地区,打造了艾瑞泽、瑞虎、QQ和风云等知名产品品牌。同时,旗下两家合资企业拥有观致、捷豹、路虎等品牌。截至2018年12月底,公司累计销量已超过750万辆,其中,累计出口达150万辆,连续16保持中国品牌乘用车出口第一位。
公司在芜湖、大连、鄂尔多斯、常熟以及在巴西、伊朗、委内瑞拉、俄罗斯等国共建有14个生产基地,具备年产106万台整车、100万台发动机、95万台变速箱的生产能力。公司现有专业研发人员超过5500人,其中拥有博士、硕士、海外归来人员等高层次人才1200多人;引进国外知名专家、管理人员300多人;“国务院特殊津贴”7人;“国家友谊奖”专家2人;以及多位安徽省“黄山友谊奖”、“百人计划”、“外专百人计划”获得者。
“自主创新”是奇瑞发展战略的核心。通过自主创新,奇瑞在DVVT双可变气门正时技术、TGDI涡轮增压缸内直喷技术、CVT无级变速器、新能源以及智能技术等核心技术上获得突破,带动了全系产品的全面技术升级。截至2018年12月底,奇瑞累计申请专利17079件,授权专利11032件。
在“中国企业海外形象20强”评选中,奇瑞汽车三次荣获中国“最佳海外形象企业”称号,位居装备制造业第一位。2018年4月,奇瑞发布了智能化品牌战略—奇瑞雄狮CHERY LION,向智能化全面转型,致力于为全球消费者提供一种“新时代智能互联的生活方式”。
图1 奇瑞汽车股份有限公司
二、企业在智能制造方面的现状
1.信息化概况
根据公司自主领先2020战略,IT在持续支撑现有业务发展的同时,通过IT2.0战略的达成,转型为业务合作伙伴,为成为业务创新和引领者的IT3.0目标奠定基础。
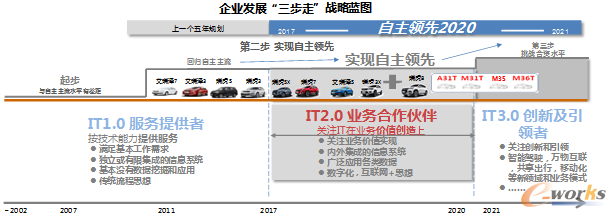
图2 战略蓝图
IT2.0围绕“一个目标,两个运营体系,三个方向,十项核心举措” ,以提升IT对企业核心价值的贡献度为目标,协同打造一个企业运营CPTO体系,通过在3个主要方向的努力,依托10项核心举措的推进,以及IT运营体系的支持,并推动企业数字化全面转型。
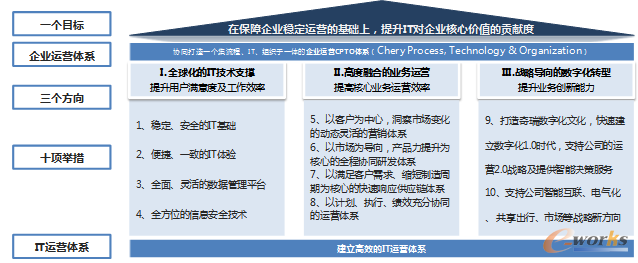
图3 系统规划
2.信息化发展历程
建设公司各业务领域的信息系统和基础设施,全面支持公司业务运作。
3.企业应用系统架构
公司整体应用蓝图以ERP、PLM等核心系统为基础,形成了包括产品研发、采购、制造、营销服务、质量、财务、人事、运营、协同9大领域。
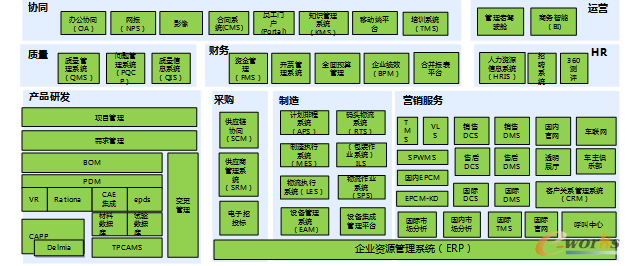
图5 应用蓝图
4.企业基础设施架构
基础设施以建立全球统一、稳定、安全的IT基础架构为目标,联通国内国际网络,从信息安全技术、企业网络/云数据中心、协同办公、大数据平台等方面全面支撑公司业务,为客户提供全球不间断的IT服务,并支撑企业数字化全面转型。
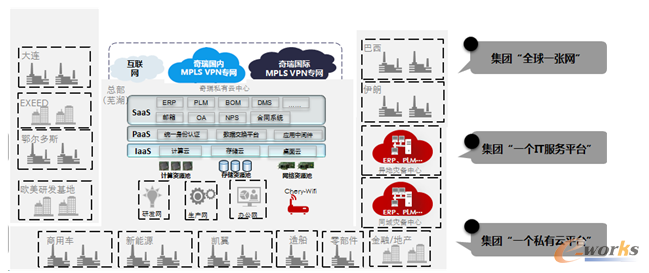
图6 基础架构
三、参评智能制造项目详细情况介绍
1.项目背景介绍
1) 业务现状分析
项目上线前,公司整车研发CAE业务流程大致分四个阶段:设计数据接收与管理、建模与仿真、分析数据存储与检索、报告发布与查询。
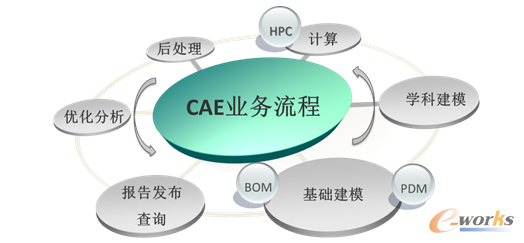
图7 业务流程图
2) 业务痛点
CAE仿真分析作为整车研发虚拟验证中关键节点之一,项目建设前主要存在以下四个方面痛点:
(1) 数据本地管理
· 建模数据线下保存,不便于版本管理;
· CAE模型和分析报告本地保存,不利于文件管理,且易丢失。
(2) 仿真建模效率低
· 目前在工作站上做网格划分,单机工作效率成为瓶颈;
· 建模工作线下沟通,沟通效率偏低;
· 新老模型对比工作量大,已有零部件模型重用效率低。
(3) 数据追朔困难
· 分析报告与产品设计CAD数据难以精确匹配;
· 整车产品CAD数据差异更新时,无法有效模型重用。
(4) 报告查阅困难
· 仿真数据的检索繁琐;
· 分析报告线下传递,数据安全难管控。
3) 项目目标
整车研发CAE数据协同平台要达成四项目标:实现CAD和CAE数据双向追溯;提高建模效率;提高分析数据管理效果;方便设计工程师查阅分析报告。
4) 解决思路
主要从系统、数据源、业务协同、知识积累四个方面进行。
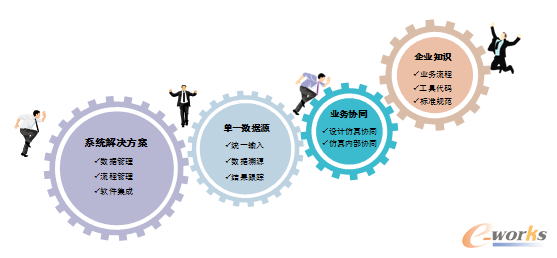
图8 解决方案
2.项目实施与应用情况详细介绍
1)系统规划及架构
图9 系统规划图
本项目分为PDM系统集成、仿真对标平台、CAE平台优化、业务流程管理优化、HPC集成五个方面进行方案规划及架构实施。
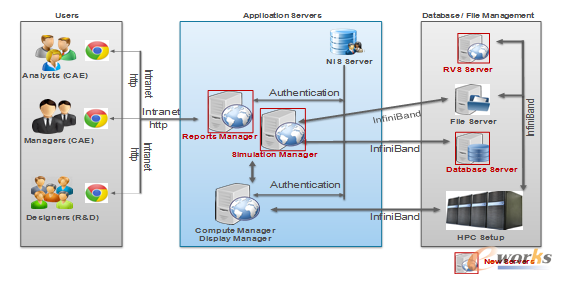
图10 系统架构图
2)项目周期
通过技术支持部门、CAE仿真分析部门、数信中心、研发技术中心,以及供应商等公司内、外部门共同合作,历时两年多,经过项目启动,方案设计、系统详细设计、系统关键用户验证等多个阶段,最终完成系统上线。期间,攻克多方面多类型技术难题,系统上线后基本实现项目目标,为跨部门数据协同应用提供基础支撑。
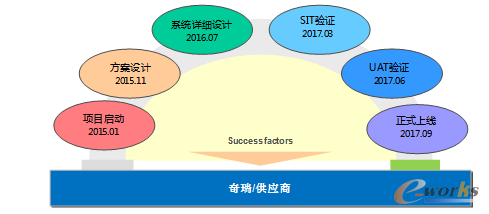
图11 项目周期及阶段
3)应用场景
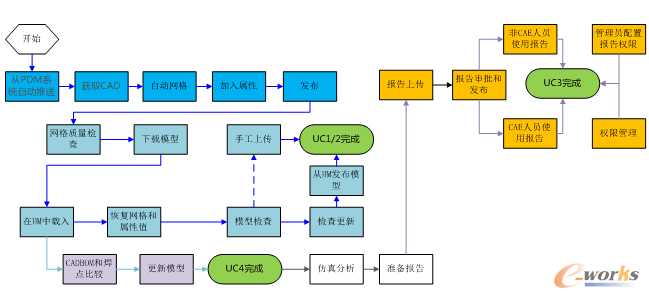
图12 系统功能整体框架图
主要包含四大核心功能:UC1—数据获取、UC2—快速建模、UC3—报告管理,以及UC4—模型更新。其中,四大核心功能中包含的重点业务场景分别参见以下章节详细内容。
(1)PDM系统端数据准备(UC1)
设计数据预检查(数字样车虚拟评审/学科多方案数据预检查)、数据预发布。
图13 系统数据管理
(2)最终提交数据检查与数据提交(UC1)
对映射完成的数据结构进行完整性、一致性检查,并提交数据下发通知。
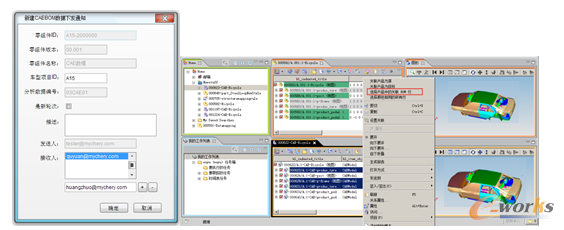
图14 CADBOM结构对比
(3)SDM(仿真分析平台)端数据获取(UC1)
如果PDM端有新的CADBOM则会自动推送到平台,包括CADBOM结构和CAD数据邮件通知用户导入完成。

图15 CAE系统端集成
(4)CAE快速建模(UC2)
自动化网格划分,属性创建, CADBOM解析,模型组装,并且支持多用户协同建模和数据文件管理的系统。
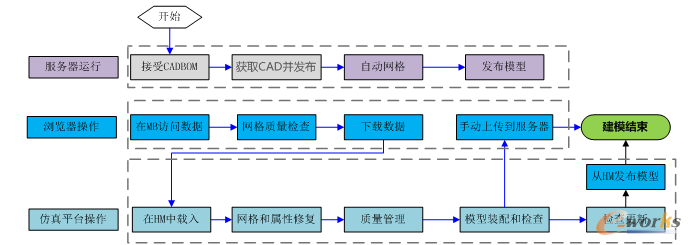
图16 CAE建模流程
(5)分析报告管理(UC3)
· 仿真报告的在SDM端的管理,包括上传、审批和查询功能;
· 提供给设计工程师的PDM端仿真分析报告查询。
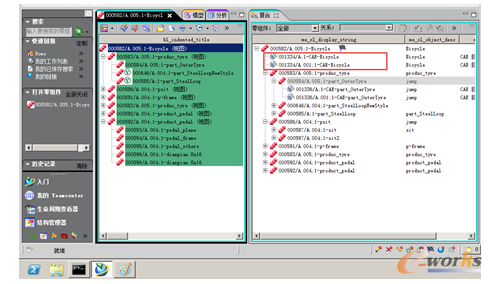
图17 查询分析报告
(6)仿真模型更新(UC4)
研发CAE仿真分析工作中有相当一部分建模工作可以靠CAE平台提高模型比较的精确度,帮助快速替换零件,生成新的模型。即把已有装配模型中的零部件替换为其他版本,以生成新的装配模型,本质上,模型替换与模型复用判断都是模型重用的范畴,即在装配中部分使用库存零件,加上新零件,组成新的有限元装配体模型。
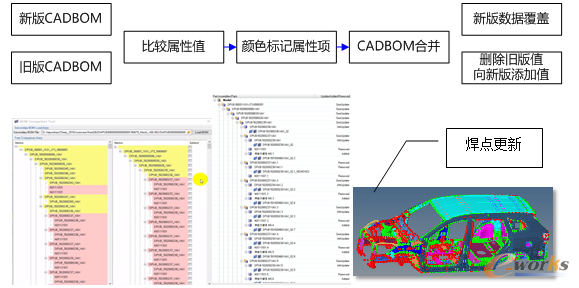
图18 结构对比及数据更新
3. 效益分析
通过本项目,构建了PDM与CAE数据协同平台,实现研发产品设计与仿真分析部门数据双向追溯,改善分析部门建模、数据管理方式,提高仿真分析建模效率,提升用户使用便捷性。
1)建立PDM与SDM连接,实现CAD和CAE数据双向追溯
· 系统间自动推送信息,获取数据,减少人工干预,年度节约达400人时以上;
· 固化CAD数据版本,性能评估结论能对应数据状态;
· 便于仿真与试验冲突时的原因分析与定位,相比上线前,缩短风险排除的时间约30%;
· 便于深入比较新老数据差异,减少无效分析,相比上线前,缩短分析周期约40%。
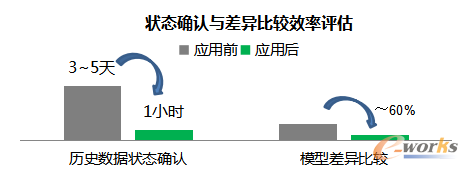
图19 CAE数据协同平台应用前后状态确认与差异比较效率评估
2)提供统一平台,方便设计工程师查阅分析报告
· 报告审批之后自动发布,并可针对特定用户发送通知信息,便于用户及时了解进展;
· 用户可从PDM客户端一键查询并浏览对应分析报告,快捷、方便;
· 从PDM端查询,免于记录、管理新的网址或安装新的客户端,更为方便;
· 从PDM端查询,可免输用户名及密码,减少不必要的操作。上述分析报告沟通、查阅年度约节约400人时。
3)改进CAE分析数据的管理方式,提升用户应用体验
· 将车型-性能-系统三级管理模式缩减为车型-性能两个管理维度,降低结构识别难度;
· 实现对所有学科方向模型的管理;
· 简化报告审批与流转的操作步骤,年度节约达1600人时以上;
· 提供工作任务待处理区,实时提醒用户处理审批任务。
4)改善建模方式,提高建模效率
· 整车快速自动化建模,缩短周期,年度约减少720人时以上;
· 通过云系统,多人在线协同;
· 提升建模规范化与标准化水平。
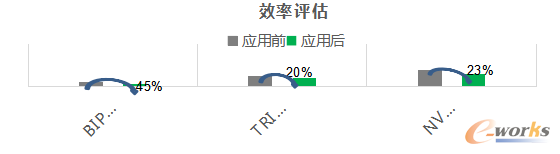
图20 CAE数据协同平台应用建模效率评估
ANSYS软件,MENTOR软件,MSC软件,仿真培训及咨询----武汉恩硕科技有限公司 服务热线:400- 6600- 365
地址:湖北省武汉市武昌区和平大道三角路水岸国际一号楼2611